Switzerland consumes more natural resources than the global average, mainly due to its high levels of prosperity. Public bodies, research institutes, companies and citizens are taking action to reduce their impact on the environment and society. Businesses are innovating and developing technologies for resource management, refuse collection and recycling more effectively with a view to creating a more circular economy.
Global population growth is inevitably putting greater pressure on natural resources. It is therefore essential to find a balance between society’s economic needs and the needs of the global ecosystem so that we can fully transition to a system of sustainable development encompassing the environment, the economy and society.
With greater energy efficiency needed in future, recycled waste is becoming an important source of raw materials. With this in mind, traditional waste treatment plants are now being converted into thermal recycling facilities. This is clearly the shape of things to come, with towns and cities ultimately being exploited as urban mines. Through recycling, urban areas will generate the metals and other materials needed for society to function.
Selfrag
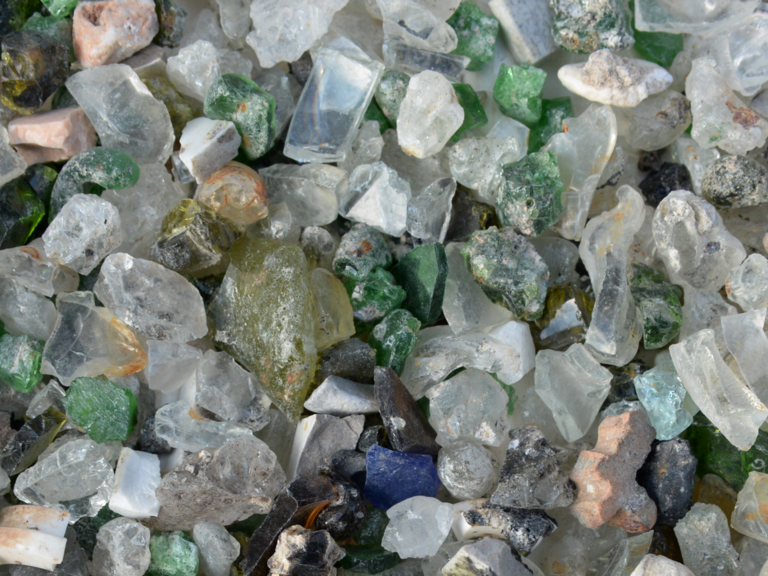
The power of lightning boosts recycling
The Swiss company Selfrag aims to minimise the amount of waste that is not recycled. Its unique high voltage pulse power electrical discharge technology reproduces the effect of lightning when it strikes a tree. This controlled fragmentation process makes it possible to separate different materials, before they are reintroduced into the manufacturing cycles. It pushes the recycling chain to its furthest limits, extracting metals such as copper, lead, tin, zinc and aluminium from the incineration residues from waste treatment plants. Selfrag has been deploying this technology in Switzerland since 2017. There are plans to introduce it in countries such as Germany, Scandinavia and the United States, which incinerate large quantities of household waste. The slag produced when household waste is incinerated contains precious materials. For example, a tonne of waste recovered from incineration plants contains an average of 7 kilograms of copper. The process enables this type of valuable material to be recycled, while at the same time reducing the amount of slag by around a quarter. Selfrag will eventually be able to cut the amount of slag in half. With its pioneering technology, the company is making it possible to recycle the ‘waste of waste’, extending the concept of recycling as far as it can go.
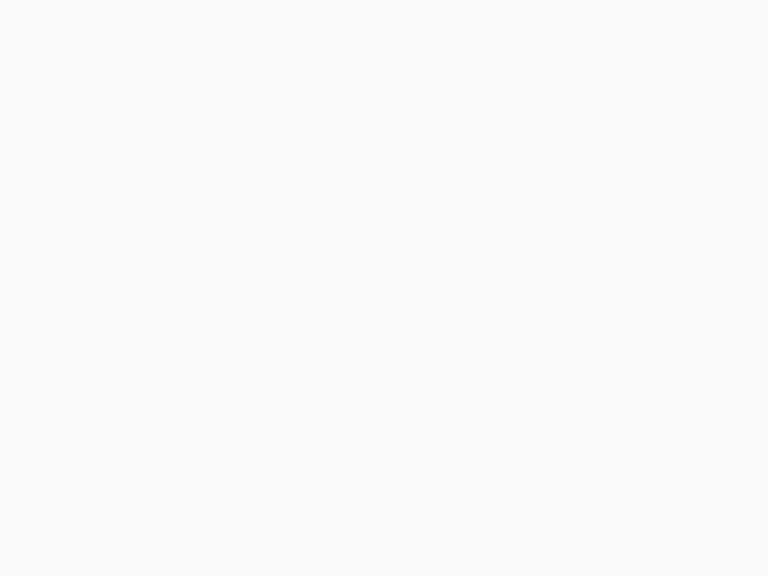
UHCS
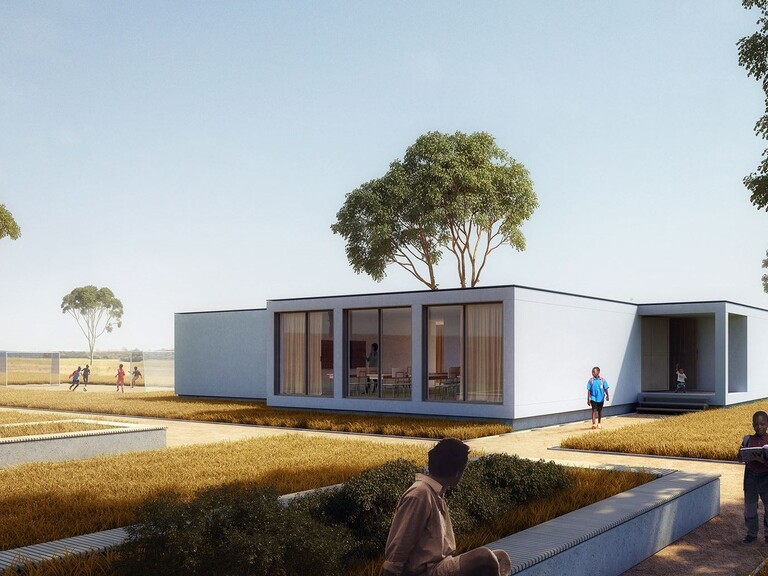
Modular houses made from recycled PET
Ustinov Hoffmann Construction System (UHCS) is developing a modular composite construction system based on recycled PET. It’s designed for industrial-scale production by extruding patented composites. Assembled like lego bricks, the composites form a cubic post-and-beam structure and load-bearing walls adaptable to different cultural traditions. This system makes it possible to build high-quality housing ecologically, lessening the impact of human needs on nature and the carbon footprint of the houses built. After a demonstration cube, the first pilot building was constructed in 2023. Others will follow, around the world. UHCS opts for recycled PET for its structures because PET can be regenerated and recycled again. Its characteristics, non-toxicity and worldwide availability make it a well-founded choice, although UHCS does occasionally use other plastics better suited to particular climatic or regional conditions. Modular manufacturing facilitates cost-effective, large-scale industrial production while complying with the most demanding static and architectural standards. Its ease of use also creates space for architectural freedom and creativity.
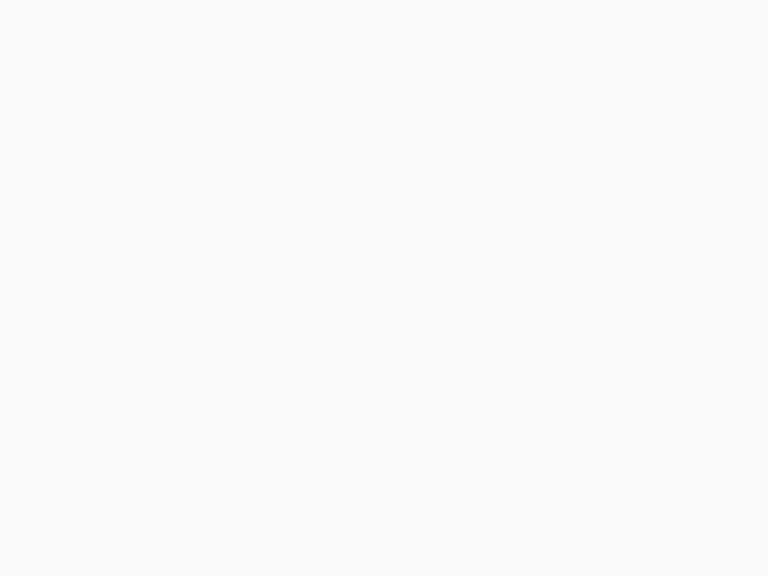
BioApply
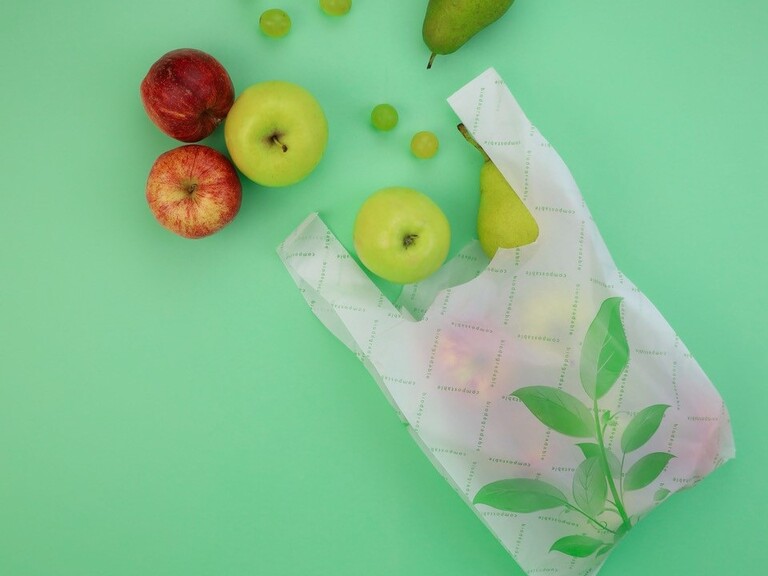
Redefining retail and waste bags
The plastic bag – a symbol of convenience with a stark environmental cost: produced in five seconds, used for 20 minutes, but persisting in the environment for over 500 years. Swiss-based BioApply is tackling this challenge by producing biodegradable bags. As plant-based alternatives, these bags optimise organic waste sorting, which means less waste incineration and microplastic. BioApply’s eco- friendly products include TreeTote, wood fibre-based bags that consume 95% less water than cotton. The innovative SurfAce technology developed by BioApply enhances biodegradable film, reducing thickness by 30% and improving durability. The company works to further the UN’s SDGs by promoting biodegradable solutions for combating plastic pollution. It has started to expand beyond Switzerland, establishing partnerships globally. With BioApply, a future with reduced plastic waste and enhanced environmental health is not just a vision – it is a reality.
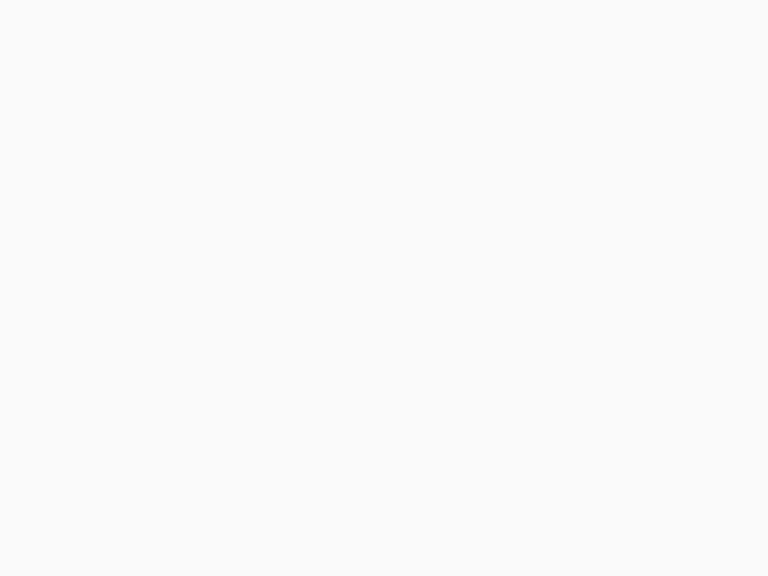
Tyre RecyclingSolutions
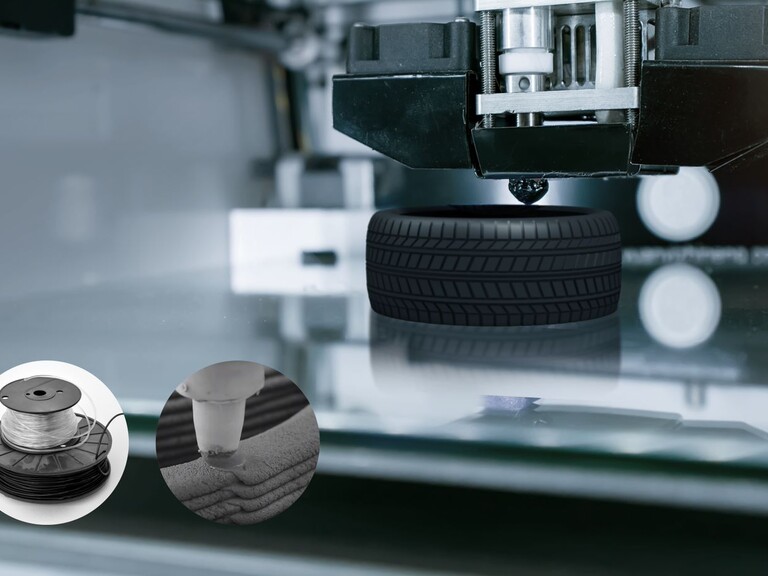
Giving Used Tyres a new Lease of Life
Each year, approximately two billion used tires need to be disposed of worldwide. Tyre Recycling Solutions (TRS) is a leading innovator in the recycling of end-of-life tires, transforming them into sustainable, high-value rubber powders, compounds, and thermoplastic elastomer materials. TRS offers a comprehensive suite of technologies, including TRS Water Pulse™—a proprietary technology that uses ultra-high pressure water jets to process the tread into rubber powders, powder activation technologies for incorporating rubber powders into asphalt, engineered compounds that mix recycled plastics with recycled rubber powders, and a laboratory dedicated to developing formulations in close collaboration with customers. TRS’s mission is to provide the market with innovative technologies that produce more profitable, high-performance, and sustainable materials, aiding the industry in transitioning to a circular economy and reducing its carbon footprint.
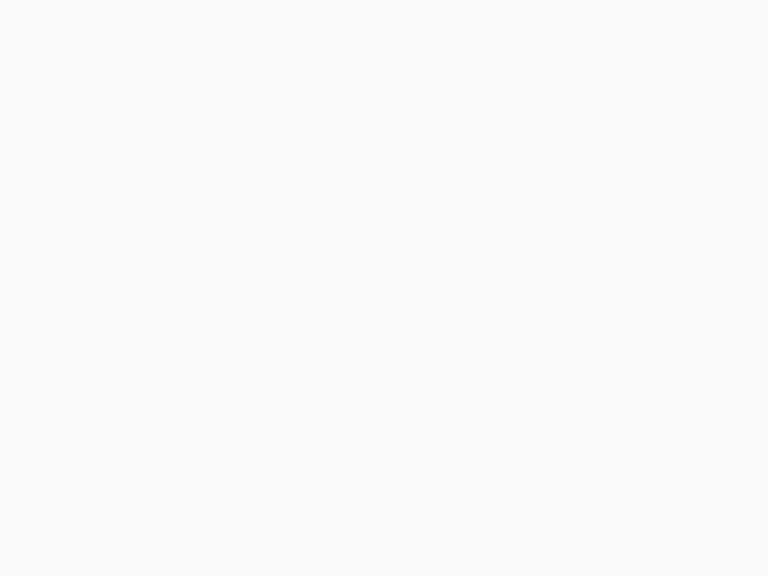