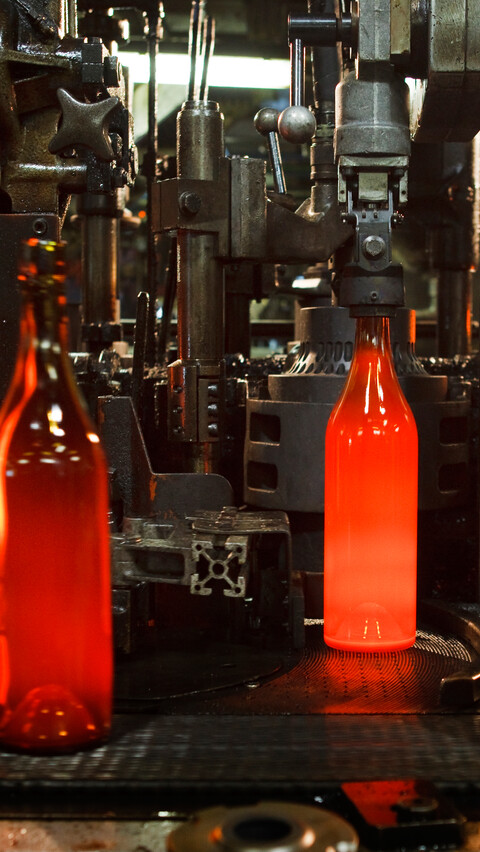
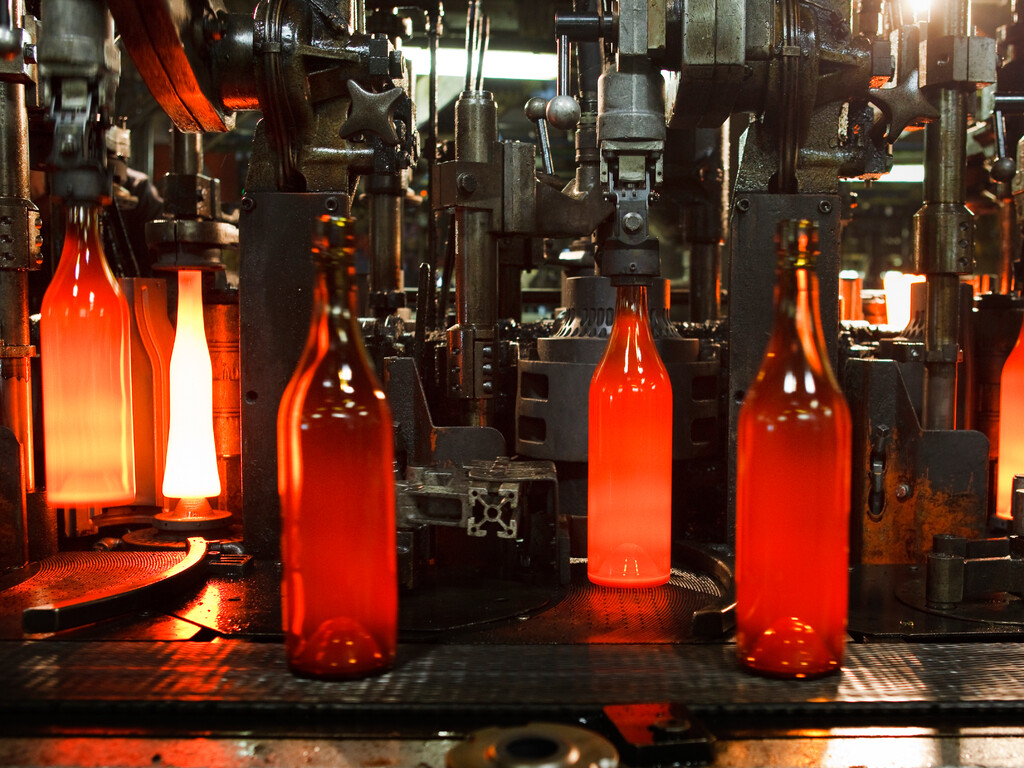
Cleantech - Circular Economy
Evolving from a linear society towards greater sustainability
The circular economy is attracting growing interest around the world, particularly in Europe, in response to the challenges facing industrial sectors. Today’s annual global economic activity consumes almost twice the resources that the planet is capable of producing and regenerating in one year. This makes it urgent to transform our business models and consumption patterns.
The shift from a traditional linear economy (extracting raw materials, consuming the products manufactured, and disposing them by incineration or in a landfill) to a more circular economy (where these products are ultimately collected, then reconditioned and re-introduced into the economy) requires a radical overhaul of business models and drastic changes in consumer behaviour. Switzerland has been a pioneer in waste treatment for many years, focusing primarily on (thermal) recycling. With all their success in building up this processing capacity and developing these technologies, the Swiss have to some extent neglected to tackle the volume of waste, which is the root of the problem. But there is now movement in this area, towards an inclusive approach that welcomes all actors wishing to get involved.
One important point to remember is that the circular economy is not based solely on recycling: moving away from the linear economy, transforming current business models and consumption patterns, and keeping products and components in the economic system for as long as possible are the real challenges of the circular economy. Although it seems that more progress has been made in some sectors (such as agri-food, construction and consumer goods) than in others (luxury goods, watchmaking, finance, tourism, etc.), each one of them can already offer at least a few inspiring examples. A wealth of best practice exists and is being developed in Switzerland. While there is still a long way to go, with a great deal of work to be done and improvements to be made, the course has been set. Switzerland will share its best practices, working with partners to develop solutions and promote their use around the world.
Oxara
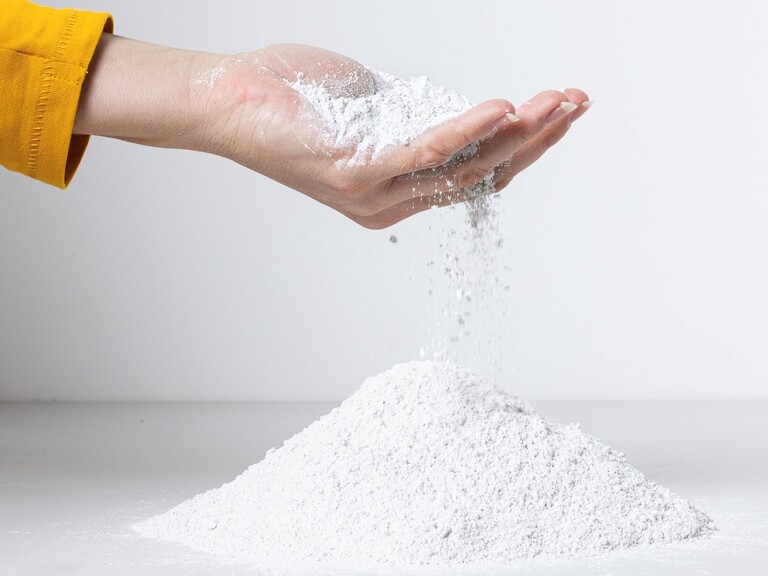
Excavation waste worth its weight in gold
Excavation waste worth its weight in gold Oxara empowers material producers to turn excavation waste into concrete by offering cement-free admixtures to produce low-carbon and circular concrete. Beyond the substantial environmental benefits, including the significant emissions reduction achieved by avoiding cement use, Oxara’s innovation also offers compelling financial benefits. At scale, the product is 10–20% more cost-effective compared to conventional concrete. Materials powered by Oxara’s innovation can be used for buildings’ structural and non-structural elements. Moreover, this solution addresses a looming challenge in the construction industry: the scarcity of raw material.
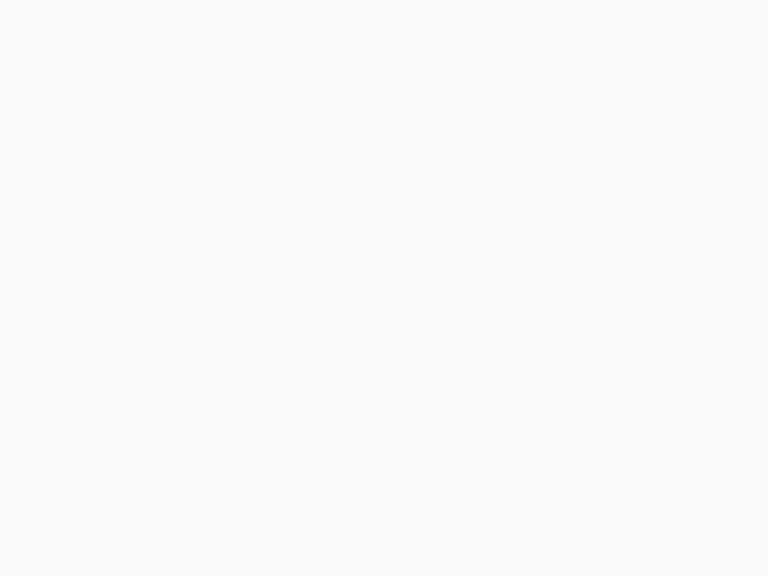
DePoly
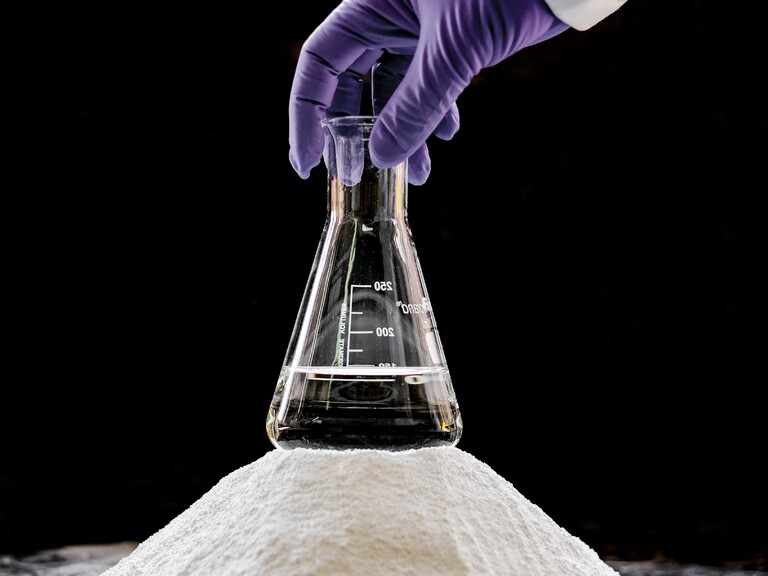
Rethinking recycling –Plastics made pure
PET is everywhere: in our clothes and shoes, in packaging, in throw-away products, and more. But the lion’s share of PET cannot be recycled using traditional methods due to potential contamination by foodstuffs, dyes or mixtures with other plastics. DePoly has developed a PET recycling process that does not require pre-washing or separation from other plastics. The method involves deploying chemical depolymerisation to use existing PET instead of oil to obtain the basic building blocks (PTA and MEG) of PET in pristine quality and purity. The PTA and MEG obtained can then be used to produce recycled PET. DePoly’s demonstration plant will be capable of processing up to 500 tonnes of plastic per year. It will be built and based in Switzerland and opened in 2025. DePoly’s patented recycling technology makes a truly sustainable circular plastics economy possible.
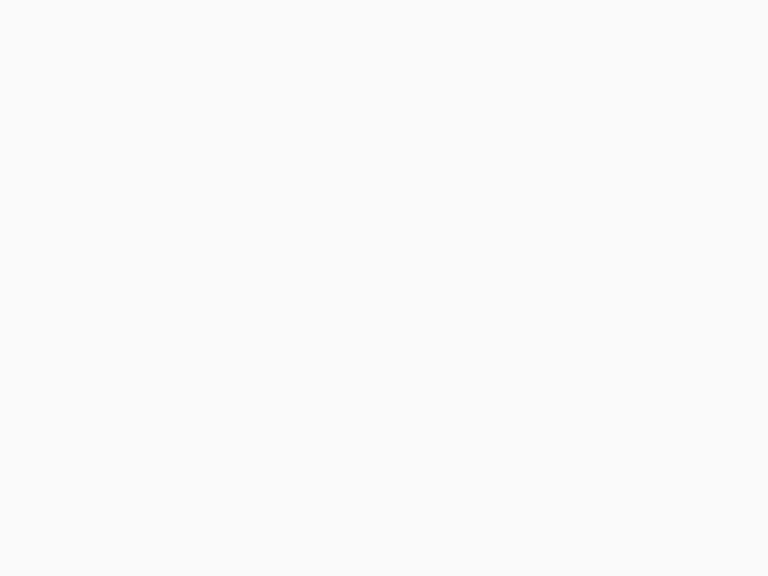
Neustark

Capturing CO2 sustainably
Neustark removes CO2 from the atmosphere by permanently trapping it in mineral waste streams such as demolished concrete. It captures carbon dioxide in biogas plants and transports it to storage sites where the biogenic CO2 is injected into granules of recycled concrete. This technology makes it possible to trap emissions there for thousands of years. The recycled, carbonised granules can be used for road construction or to produce recycled concrete. Moreover, recycled concrete’s carbon footprint is about 10% smaller because the enriched material also reduces the proportion of cement used. This innovation, already taken on board by the city of Bern, complies with all standards. Neustark concrete can be used at construction sites in the same way as normal concrete. And when demolished, the material does not release any of the CO2 it has been enriched with, as the latter has been solidified: only heating it to over 600°C turns its CO2 back into gaseous form. As of 2024, neustark already had over 20 CO2 capture and storage sites up and running, with several more under construction across Europe. The Bern-based start-up aims to eliminate one million tonnes of CO2 by 2030, with more to follow.
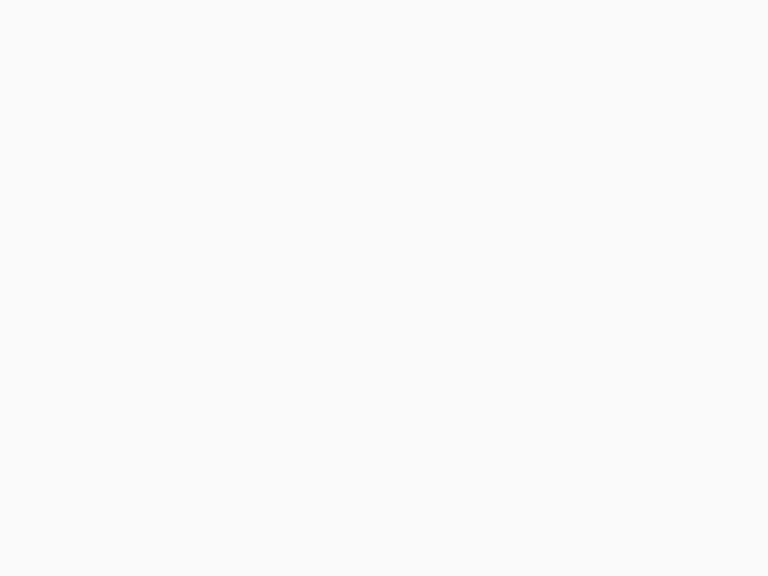
Panatere
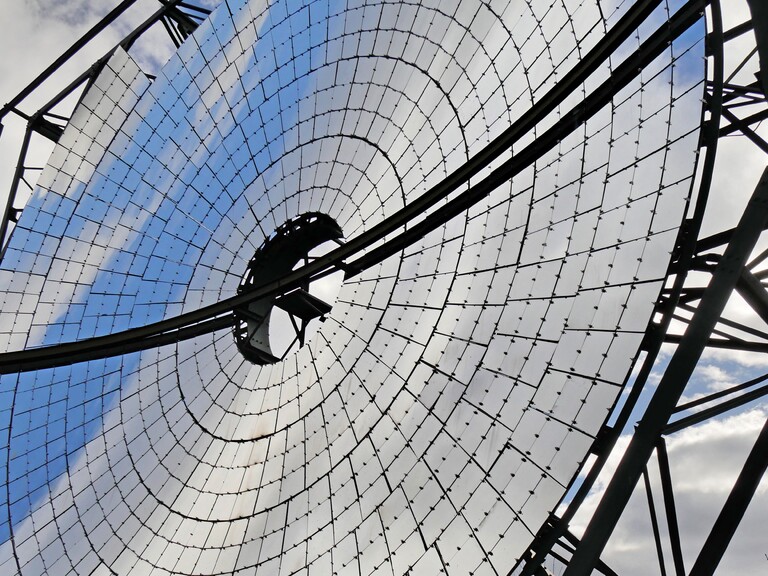
A solar furnace serving microtechnology
For years now, Panatere has been building parts and cases for the watchmaking industry as a subcontractor. These activities produce a lot of scrap steel, which ends up in the waste bin along with 10% of machined parts because of defects in the raw material. It was with this in mind that Panatere came up with the idea of recycling the steel shavings to obtain a material of impeccable quality, and integrating a sustainable energy source into the production process. The company has since produced its first ingot from a solar furnace, opening the door to production for the watchmaking and medical sectors. Sunlight, focused through concave mirrors like through a magnifying glass, brings the steel to its melting point (1,535°C). This process makes it possible to reclaim and transform scraps of raw materials using solar energy, in a 100% circular cycle.
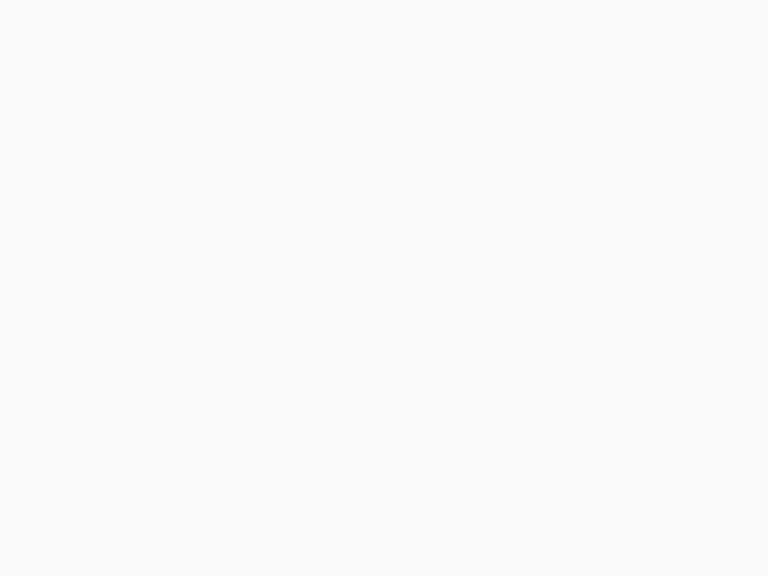